Technika Wydruku 3D (wywiad z Drygolem/Lamers)
Johny
Johny: Przedstaw się Drogi Kolego. :)
Drygol: Jestem Drygol z grupy Lamers, po prostu. ;)
Johny: Tematem wywiadu będzie technika wydruku 3D – a dokładnej stosowana przez Ciebie FFF czyli Fused Filament Fabrication.
Drygol: Dokładnie. Ok. Zaczynamy.
Johny: Co skierowało Twoje zainteresowanie w kierunku druku trójwymiarowego, jak zaczęła się Twoja przygoda z tym zagadnieniem?
Drygol: To w sumie dosyć ciekawy zbieg okoliczności. W 2012 r. poszedłem na SV2K12, bo party odbywało się dosłownie dwie ulice dalej od mojego miejsca pracy. Oprócz tego, że spotkałem masę ciekawych osób (...i ponownie wkręciłem się w tematy związane ze starszymi kompami), to spotkałem też Jakuba Husaka, który właśnie drukował na swoim RepRapie różne znaczki. Jak tylko spojrzałem na tę maszynę, to oczy mi się zaświeciły. :) Zacząłem zadawać Kubie sporo pytań. Jak to działa, na jakiej elektronice, jaki soft itp. Później to już niestety party-flow mnie trochę porwał. ;P
Jakiś miesiąc później robiłem modyfikacje swojego Atari 65XE. Oprócz całej masy modów miała też być nowa klawiatura podświetlana na niebiesko. Długo szukałem różnych klawiatur, ale nie znalazłem żadnej, która by miała podobne kołki w klawiszach, co te oryginalne w Atari. W pewnym momencie mnie olśniło, że przecież mogę sobie zbudować drukarkę 3D i wydrukować odpowiednie kołki. Tak to się wszystko zaczęło.
Johny: Czy miałeś jakąś pomoc merytoryczną w tej dziedzinie, czy ktoś pomógł Ci w początkowym okresie zgłębiania zagadnienia?
Drygol: Tak, jak już wcześniej wspomniałem, pierwszy kontakt to Kuba Husak, który mnie nakierował na odpowiednie website`y i fora. Dalej to już sam działałem. Parę razy jeszcze pytałem Kubę o jakieś niuanse, których nie pamiętam, ale raczej temat już leżał po mojej stronie.
Johny: W jaki sposób pokrótce zbudowałeś swoją pierwszą drukarkę?
Drygol: Pierwsza konstrukcja, czyli Prusa-Mendel, opierała się o części drukowane kupione od Kuby. Reszta części to juz Castorama, Allegro i złom elektroniczny, który jak każdy prawdziwy nerd niezłomnie zbieram. Jeżeli chodzi o samą budowę, to jest to konstrukcja składająca się z prętów gwintowanych połączonych częściami drukowanymi z plastiku. Elektroniki jest aktualnie na rynku cała masa, ale w 2012 r. tak dużo do wyboru jeszcze nie było. Ja zaczynałem od elektroniki o śmiechowej nazwie Sanguinololu - jest to właściwie płytka z układem Atmega1284P i z portami pod tzw. StepSticki, czyli pod układy kontroli silników krokowych oraz wyjściami pod endstopy, grzałki i termistory.
Kompletowanie części zabrało mi około 2 tygodni. Potem po kolei zaczęło się składanie. Rama, osie XYZ oraz montaż ekstrudera. Później okablowanie i elektronika i... miesiąc kalibracji. Teraz, jak już znam temat, to zajmuje to ze 2 godziny, ale wtedy było to trochę po omacku i szło żmudnie.
Johny: Co w tej pracy generowało największe problemy?
Drygol: Właściwie to cały czas generuje. Mając już jakieś doświadczenie w tej materii to zaryzykuję stwierdzenie, że właściwie sama budowa drukarki to łatwa sprawa. Schody zaczynają się w momencie przygotowania obiektów do druku. Wchodzi tu cała masa parametrów. Chodzi zarówno o fizykę topnienia materiałów z których powstaje wydruk, jak i różne metody cięcia i ułożenia modeli na stole. Nie wszystko jest łatwe w druku... właściwie to mało jest modeli łatwych. Można śmiało powiedzieć, że dobry wydruk to w 70% umiejętności drukarza, a 30% to sprzęt.
Johny: Pierwszy wydruk - co to było - jak się wydrukowało?
Drygol: Nie jestem pewien, ale wydaje mi się, że były to części zapasowe do drukarki. Chwilę później drukowałem już drugą drukarkę. Drukuje się to dosyć prosto, bo modele 3D poszczególnych części do drukarek są tworzone właśnie z myślą o łatwym wydruku. Tak, aby każdy n00b sobie poradził.
Johny: Materiał, którym drukujesz, pokrótce.
Drygol: Na naszym rynku są w zasadzie dwa rodzaje plastiku. Kopolimer akrylonitrylo-butadieno-styrenowy, czyli popularny ABS stosowany np. w obudowach starych komputerów oraz polimer kwasu mlekowego, czyli w skrocie PLA. Są tez inne ciekawe materiały, ale dopiero zaczynają wchodzić na nasz rynek np. laywood, który w znacznym procencie zawiera pył drewniany, a wydruki przypominają drewno, Laybrick (przypominający gips) czy też różne odmiany nylonu.
Swego czasu znajomy drukował z żyłki do podkaszarek zakupionej w Leroy Merlin, bo jest to po prostu nylon. Każde z tych tworzyw ma swoje zalety i wady oraz różne stopnie trudności w drukowaniu. Dla przykładu, ABS drukuje się na podgrzewanym do 90-100 stopni stole, ponieważ zbyt duży skurcz wystudzający mocno odkształca wydruk (tzw. warping) i w efekcie otrzymujemy krzywe coś, co miało być proste. :) W PLA ten problem nie występuje i właściwie nie potrzeba grzać stołu, natomiast wydruk z PLA nie nadaje się do użytku w temperaturach powyżej 120 C, bo zaczyna się odkształcać. Nylon z kolei trudno przywiera do stołu i często w połowie wydruku lata z całą głowicą. Ja drukuję głównie w ABS. Lubię ten plastik przede wszystkim ze względu na możliwość późniejszej obróbki w oparach acetonu, co ładnie wygładza powierzchnie.
Johny: Przygotowanie obiektów do druku – jak wygląda?
Drygol: W świecie druku 3D przyjął się format obiektów STL. Tworząc swój obiekt w dowolnym programie należy pamiętać, żeby eksportować właśnie do STL-ki.
Ja głównie pracuję na oprogramowaniu open source, ale komercyjne programy często umożliwiają zapis w tym formacie bezpośrednio lub przez różne pluginy.
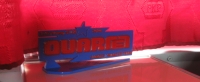
Na dobry początek trzeba się zastanowić, jak obiekt będzie drukowany, tj. w jakim układzie. Głównie chodzi o to, aby drukować jak najmniej w "powietrzu". Eliminuje się dzięki temu tworzenie tzw. supportów, czyli wydruku pomocniczego, który pójdzie na straty. Czyli przygotowujemy odpowiednie ułożenie obiektu 3D względem osi XYZ. Następnie taki obiekt należy wczytać do oprogramowania typu slicer. Druk 3D w technologii nakładania warstw polega na podnoszeniu osi Z o zadaną wartość np. 0.2 mm i właśnie na takie slice`y trzeba dany model pociąć oraz wygenerować G-code, czyli instrukcje stosowane w maszynach CNC. W tym wypadku G-code będzie składał się z instrukcji wysterowania silników poszczególnych osi oraz ekstrudera. Mając wygenerowany G-code należałoby go jakoś przesłać do drukarki. Tutaj jest kilka opcji i jak zwykle problemów. Ponieważ spora część elektroniki używa popularnego FTDI, to jesteśmy przeważnie ograniczeni do transmisji o prędkości 115200 baud. Mając więc G-code o rozmiarze np. 20 MB robi się smutno. Elektronika często musi czekać na dane, przez co na bardzo krótkie chwile zatrzymuje głowicę. W tych miejscach powstają później tzw. bloby, czyli plastik, który grawitacyjnie wycieka z głowicy. Sposobem na to jest dołożenie karty SD i drukowanie z niej bezpośrednio. Firmware bez problemu obsługuje taką opcję. Jeżeli nie mamy układu z kartą SD, to niestety zostaje nam użycie oprogramowania typu Host Controller. Zaczytujemy G-code, wciskamy start i zamykamy oczy.
Johny: Jakie jest zastosowanie praktyczne druku 3D?
Drygol: W technologii FFF (Fused Filament Fabrication) jest trochę ograniczeń. Oczywiście istnieją rożne inne technologie druku, które mają mniejsze ograniczenia, ale ja na razie skupię się na FFF. Na tę chwilę główne ograniczenia to właściwie wielkość stołu do drukowania, bo przeważnie jest to 200x200 mm. Kolejnym utrudnieniem jest czas druku. Duże wydruki potrafią się rzeźbić po kilka godzin. Rozdzielczość jest też w pewnym stopniu problemem, ale są na to rożne sposoby. Poza wymienionymi jest jeszcze kilka pomniejszych problemów, ale plusów wynikających z możliwości zmaterializowania właśnie narysowanego na kompie obiektu jest dużo więcej.
Dla mnie pierwszym praktycznym zastosowaniem były wspomniane na początku pady do klawiszy do Atari. Później drukowałem sobie elementy do samochodu, które się połamały. Można drukować zarówno ozdoby, jak i różne obudowy, wieszaki, części do innych maszyn, a przede wszystkim prototypy. W razie potrzeby można wydrukować negatyw formy gipsowej i robić odlewy z metalu. Możliwości jest mnóstwo.
Johny: Jakie są zatem zalecenia/propozycje dla potencjalnie zainteresowanych drukiem 3D?
Drygol: Jeżeli chodzi o radę ode mnie, to zdecydowanie polecam zbudować drukarkę samemu, a nie kupować KIT do złożenia, czy co gorsza gotową drukarkę. Sporo ludzi zaczyna od gotowych drukarek i po chwili się zniechęca, bo nie rozumie zasady działania poszczególnych elementów, przez co ich wydruki są kiepskie mimo wydania 3 czy 5 tysięcy na sprzęt. Sądzę, że tanią drukarkę 3D można we własnym zakresie zbudować za maksymalnie 1100 zł i będzie całkiem fajnie działać. Oczywiście apetyt rośnie w miarę jedzenia, więc na tym się nie skończy – zapewniam. Zapraszam do przejrzenia strony http://reprap.org celem wyboru modelu drukarki 3D na pierwsze zabawy. Jeżeli chodzi o moje wypociny, to oprócz innych projektów można zobaczyć 3 iteracje moich drukarek pod adresem https://vimeo.com/pithax/videos.
Johny: Dzięki za wywiad. Wnioskując – drukowanie 3D metodami quasi-domowymi jest z powodzeniem możliwe. Wystarczy tylko posiąść odpowiednią wiedzę, przygotować się technicznie i można działać na tym polu z sukcesami, o czym świadczą poczynania mojego rozmówcy.
Drygol: Również dziękuję - Lamers - gotujemy w folii.
Wywiad przeprowadził Johny/Lamers.
6 stycznia 2015 r.